Screw driver Technology Selection
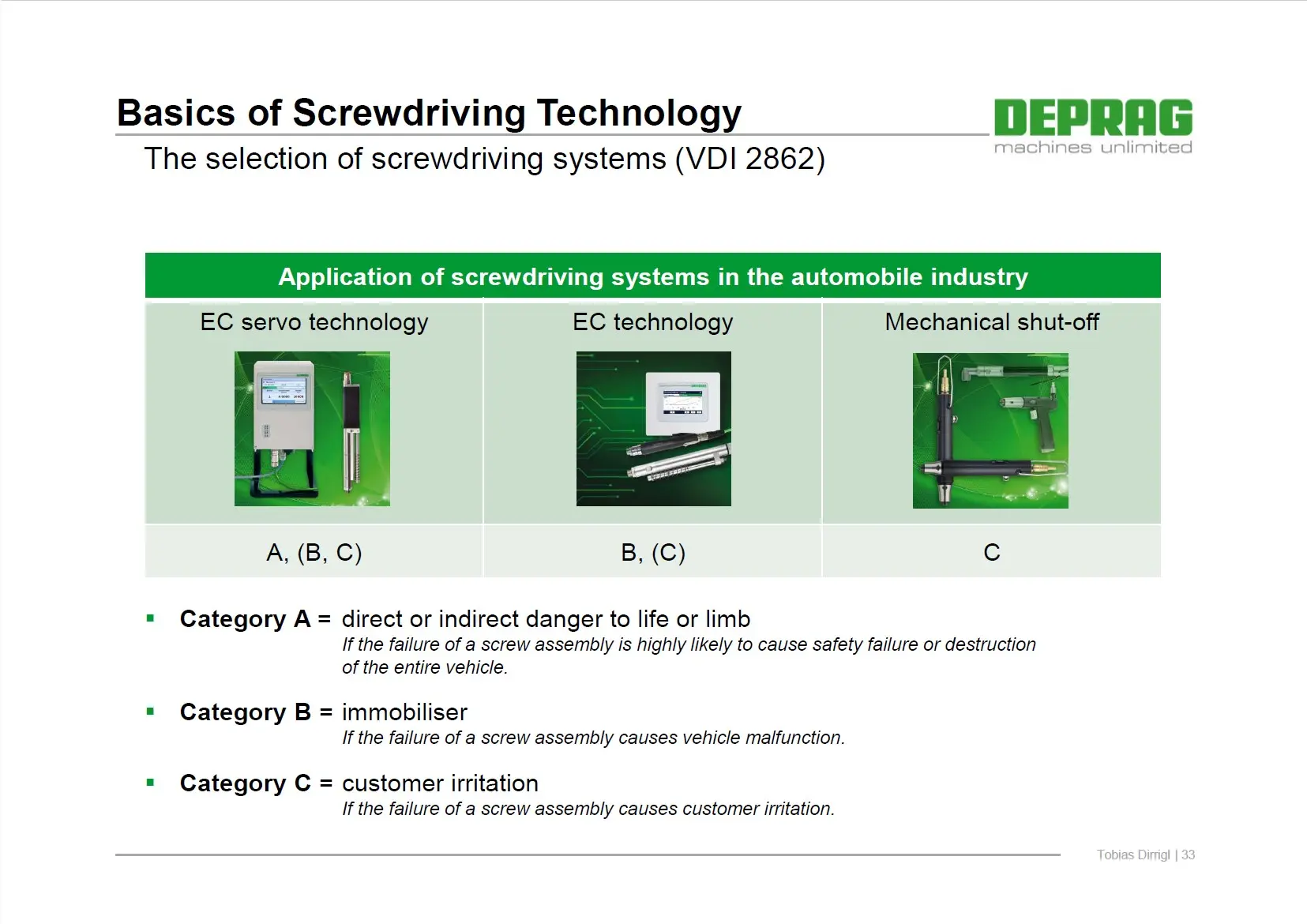
Flow Drill Screws, Flow Form Screws
FDS® screws from EJOT and FFS® screws from Arnold have been around for a while. They offer the benefits of a secure and strong joint from one side between two sheet metals. A big advantage is that they can join dissimilar materials like aluminium, steel and plastics where spot welding is not possible (they are finding more and more applications in the automotive industry where aluminium and other materials need to be joined). They also allow the use of thinner sheets without the use of additional hardware to strengthen the joints (this is making them more popular in the whitegoods industries).
The screws form a hole by high pressure and the speed of the screw, the heated material is then threaded and cools around the screw. The joint is strong, and the unscrewing torque is high. The thread formed is upto 3 times thicker than the sheet metal.
Advantages for joining sheet metal:
It seems more and more big brand manufacturers are getting their tools made in China or India with substandard materials and design but still charging premium prices.
We recently decided to offer the PB Swiss Tools range of hand tools. They offer a no compromise, top-of-the line range of hand tools, 100% made in Switzerland. They use the highest quality steels, they feel fantastic in your hand, look great (professional) and they last a lifetime. We have uploaded a selection of their various screw assembly related hand tools, but the full range also includes striking tools (mallets, punches, chisels etc) as well as special tools like picks, scribes, awls, hose pluckers and titanium tools.
Screwdrivers:
PB Swiss Tools screwdrivers feature the distinctive Swissgrip handles as well as precise, high quality steel drives.
The Swissgrip handle is made of two components. It feels good in your hand, is slip free, resistant to oils and provides grip even if you have wet hands.
Allen Keys: Available in sets or individually.
For every Allen key, the tolerances are guaranteed to be less than a hair width. This perfect dimensional accuracy and the hard and tough special alloying make for precise, durable tools.
Available finishes include:
T Handle Wrenches:
Okay so we are biased, but these have to be the best T handle wrenches on the market! They are tough, the handles are ergonomic – soft non slip grip and they look the goods.
Ratchet Drivers:
The ideal tool for fast tightening & loosening of screws featuring the famous Swiss Grip handles. Unlike most other ratchet screwdrivers, these are made to be used every day as you favorite tool, and to outlast your car!
Torque controlled screw tightening has always been the most reliable and easily applied method to produce a quality screw joint. But is torque control really going to give the perfect assembly every time?
Firstly, what is a perfect screw joint? What do we want to achieve by assembling a screw in a product?
We normally need to join two parts together, but more than that we want to induce tension in the joint so that the parts do not come apart. Sometimes we also need to seal the parts together to prevent leakage or keep dust and water out.
So the aim for a screw joint is not simply to assemble the screw to a target torque within a set tolerance, but it is to induce a constant clamping or pre-load force.
When we apply torque to a screw joint we can calculate the amount of tension induced in the joint assuming that there is no friction in the joint. In a low friction assembly (eg machine thread screw into a pre-tapped hole) almost all of the torque will induce tension in the joint. If you know the pitch of the thread and the torque applied you can then calculate the tension.
Fluctuating screw-in torque influences pre-load force!
What about thread forming and self tapping screws? We know that a portion of the torque is lost to friction and by doing some analysis we can subtract the friction and figure out the average torque used to clamp the parts. In most cases this will be enough, but what if the friction is not the same in every assembly?
What if a screw with a thread diameter at the high end of it’s tolerance meets a part with a hole dia that is at the low end of the tolerance? In this case less torque will be used to clamp the joint and it may not be enough. At the other end of the spectrum, there could be too much torque which could strip the joint or damage the part.
The solution is Friction Tightening. The advent of EC and EC servo screwdrivers has paved the way to improving the quality of screw joints. Today we can assemble the screw, calculate the friction torque and then add the pre-determined tightening torque. So if the friction torque varies, the actual clamping torque and consequently the clamping force will still be constant on every assembly.
Using the friction torque measurement we cannot use the final torque for statistical analysis anymore. The final tightening torque is the sum of the friction torque and the clamping torque the final torque accuracy will depend on the quality of the joint and the screws. We now have to look at the clamping torque only for statistical analysis.
The friction torque method is already well established in the international automotive industry as well as the electronic, mobile technology, household goods and medical industries.
Friction tightening modules are optionally available on Deprag’s Hand Held programmable screwdrivers and machine mountable electric screwdrivers.
For more information or if you would like to discuss an application, please don’t hesitate to contact us.