What's the deal with Turbine Powered Grinders?
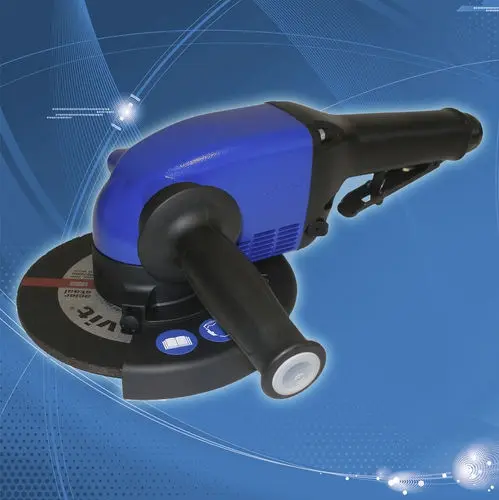
Unfortunately compressed air turbine powered grinders are overlooked by factories because of their high initial cost compared with cheaper tools. Here we are going to go through and explain some of the advantages of these grinders andd try to explain how they will actually save your organisation money in the long term.
ELECTRIC VS AIR POWER:
240V electric powered grinders are readily available and reasonably cheap, but iunder the stress of continual use an industrial quality air grinder will always outlast the electric grinder as long as it has a quality air supply. Air grinders will not be affected by dust in the air, they cannot be overloaded or overheated. The air grinder will also be lighter than an electric grinder with the same power output. Especially in the case of 230mm grinder, air grinders are available with higher power outputs. Please note! Most electric tool manufacturers quote the max power input to their tools. Air tool manufacturers quote the max power output! So a typical 1000W 240V grinder will only output 600 to 700W of power. A 1000W air grinder outputs 1000W as long as you have enough air to run it.
POWER to WEIGHT RATIO:
Often we want maximum power without the weight right? It's not helpful to have high power and high weight or low weight with low power. Higher power with lower weight means that the work is done faster and with less fatigue. Less fatigue means less chance of accidents, less breaks and less down time.
Air powered grinders are often chosen over electric tools because for a given power, the vane motor powered grinder is going to be lighter and smaller than a 240V electric grinder. Smaller and lighter tools mean that the operator is not going to be as tired, he can work longer without breaks and there is less chance of injury.
Turbine powered grinders take this a step further. For example:
HIGH POWER
Why is high power more important? Because it saves you money of course!
- Faster material removal - time is money right? If your trigger time is 3 hours per day, your extra material removal can be a tonne or more over a year compared to a vane powered tool.
- Optimal cutting / grinding speed means that your abrasives last longer - save over 30% on your abrasive costs if you are using quality abrasives!
- If low powered tools are used, the speed drops when pressure is applied resulting in faster abrasive wear. HIgh powered tools with speed governors do not slow down.
LOW MAINTENANCE COSTS
Turbine motors have all the advantages of vane motors - (cannot overload, cannot overheat, not affected by dust etc), but they do not have vanes, which is a wear part. As long as they have clean, water free compressed air, you can depend on them for a trouble free lifetime whereas vane motors have wear parts - especially vanes, that have to be replaced every so often.
ENERGY EFFICIENCY
Compressed air is EXPENSIVE. The turbine compressed air motor is already a comparatively efficient air motor (see the above comparisons) which of course means it will cost you less to run your compressor. Deprag has also taken advantage of some of the turbine motor's characteristics to make them even more efficient.
Deprag has included a speed governor in it's range of turbine grinders which means that when the tool is not under load it consumes less than half of the air that it uses when under full load. As the load increases the govenor progressively opens the air inlet valve, increasing the air supply and thereby increasing the power. The governor also maintains the correct speed no matter what the load - extending the life of your abrasives.
SUMMARY
To really understand the value of turbine powered angle grinders you need to look past the initial cost, especially if grinding is a big part of your business. The lifetime cost of every tool has to be considered. Compressed air, abrasives and man-hours are not cheap and they all add up over time. Many companies have done the tests and have come to realise that the savings we are talking about are real and significant. Don't ignore the facts!
Take a look at the Deprag 230mm Turbine grinder in action here: https://youtu.be/sufhzTdhMso